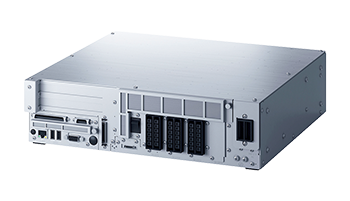
The world’s smallest* lightweight, high performance 8-axis controller that offers a high degree of freedom in installation to save space.
Compact Size
The world’s smallest* lightweight, high performance 8-axis controller that offers a high degree of freedom in installation to save space.
- Lightweight: 10 kg
- Space-saving cable
*As of November 2011, in-house research for robot controllers supporting six-axis robots (3 Kw class)
Exceptional Usability
Improved GUI for Increased Efficiency
- A clearer, more logical menu structure and improved usability.
- Improved GUI and control functions reduce time required to implement a robot.

I/O VIEWER
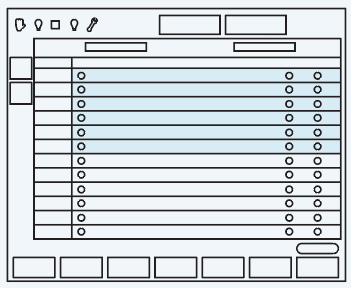
VARIABLE VIEWER
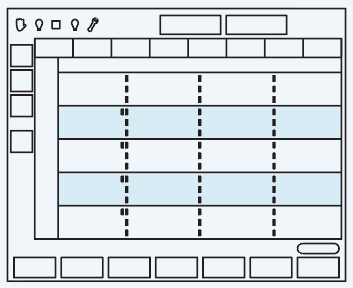
SERVO MONITOR
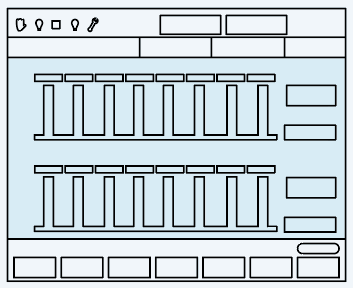
CONTROL LOG
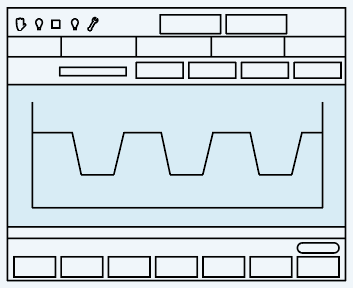
TEMPLATE
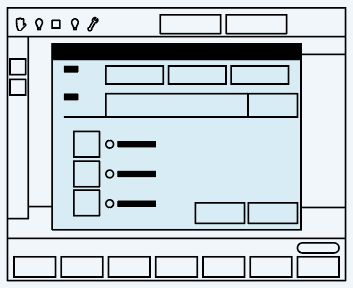
ERROR LOG
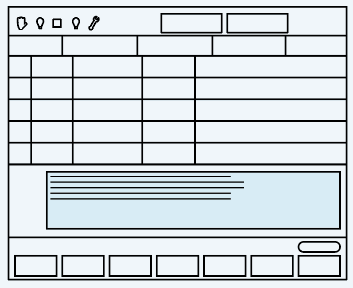
Compliance with Global Standards
Leveled specifications and standards to improve variability 80% of global share networks supported.
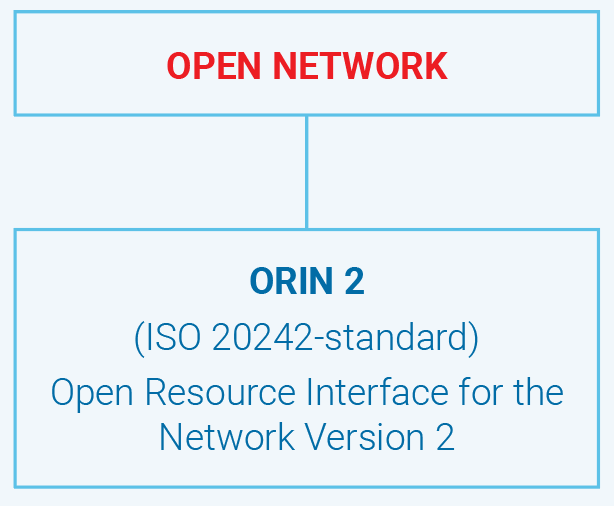
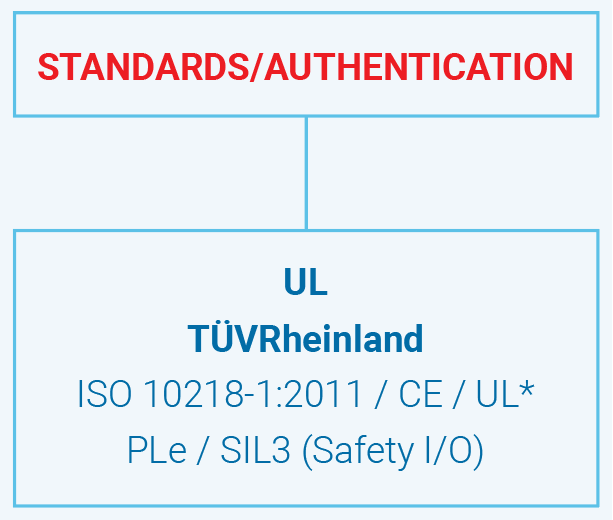
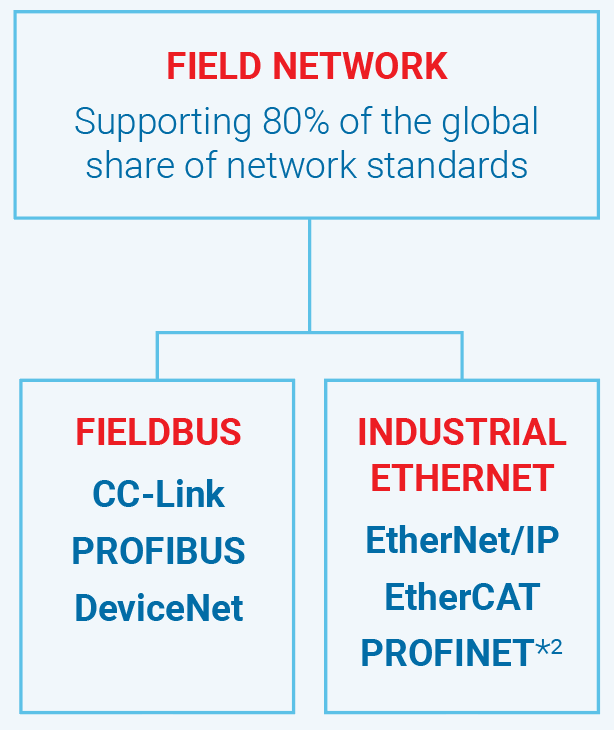
Wide Expandability
Many different devices can be connected and controlled to meet a wide range of needs.
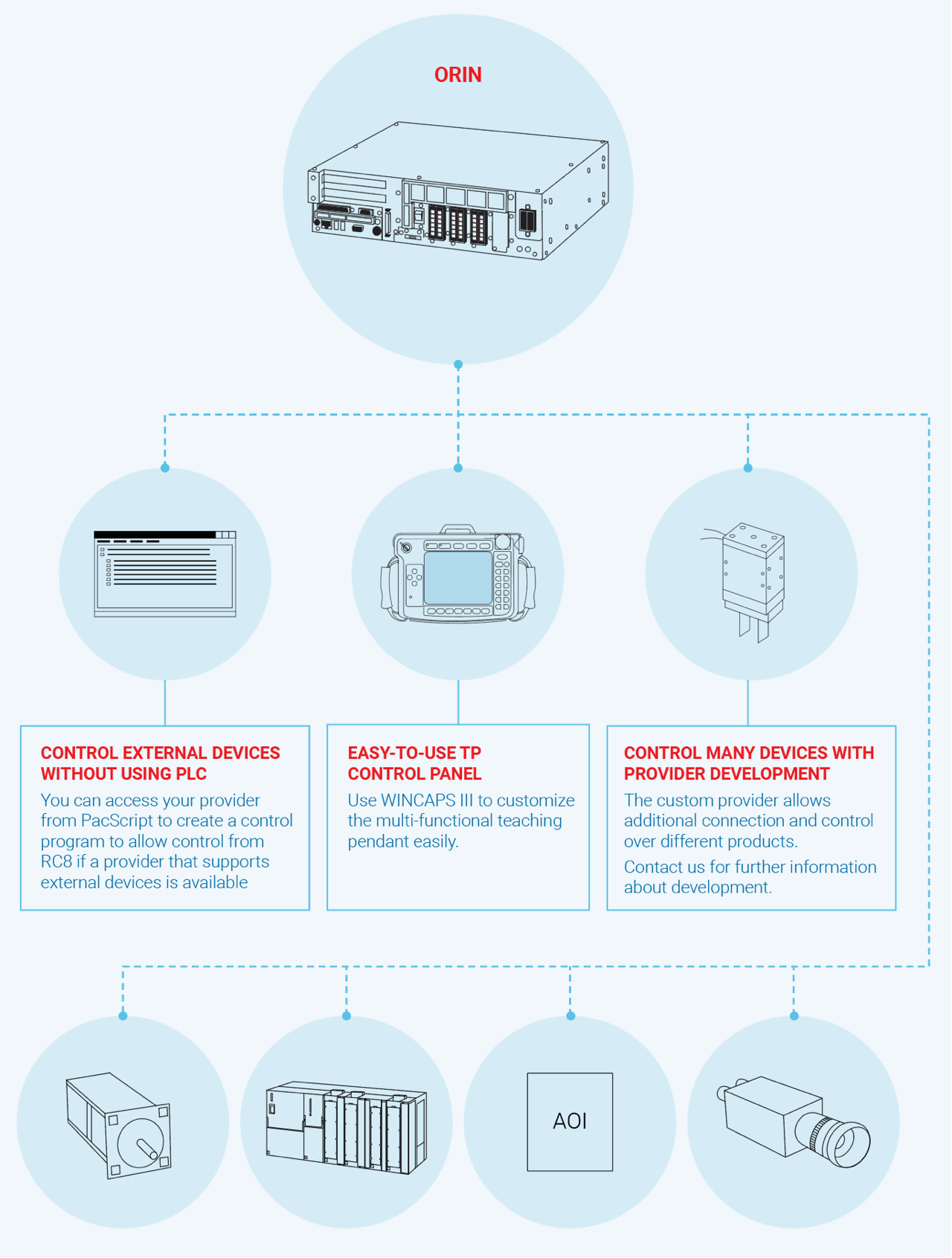
Safety Motion Function (optional)
Working near DENSO robots safely is possible thanks to the Safety Motion function of the RC8A robot controller. This function enables users to define virtual fences around the work environment and thus regulate the robot’s activity when a person enters into predefined safety zones.
The Safety Motion function is a cutting-edge tool for maximizing industrial robot safety and is offered as an with the RC8A robot controller. Optical sensors are employed to dynamically control robot speed in relation to the distance of approaching individuals, making working environments with robots safer for humans. The sensors — one placed at the bottom and one at the top of the automation cell — generate virtual safe zones. Zones A and B are farthest from the robot and Zone C is closest. Entry into Zones A or B triggers speed reductions, while entry into Zone C stops the robot entirely.
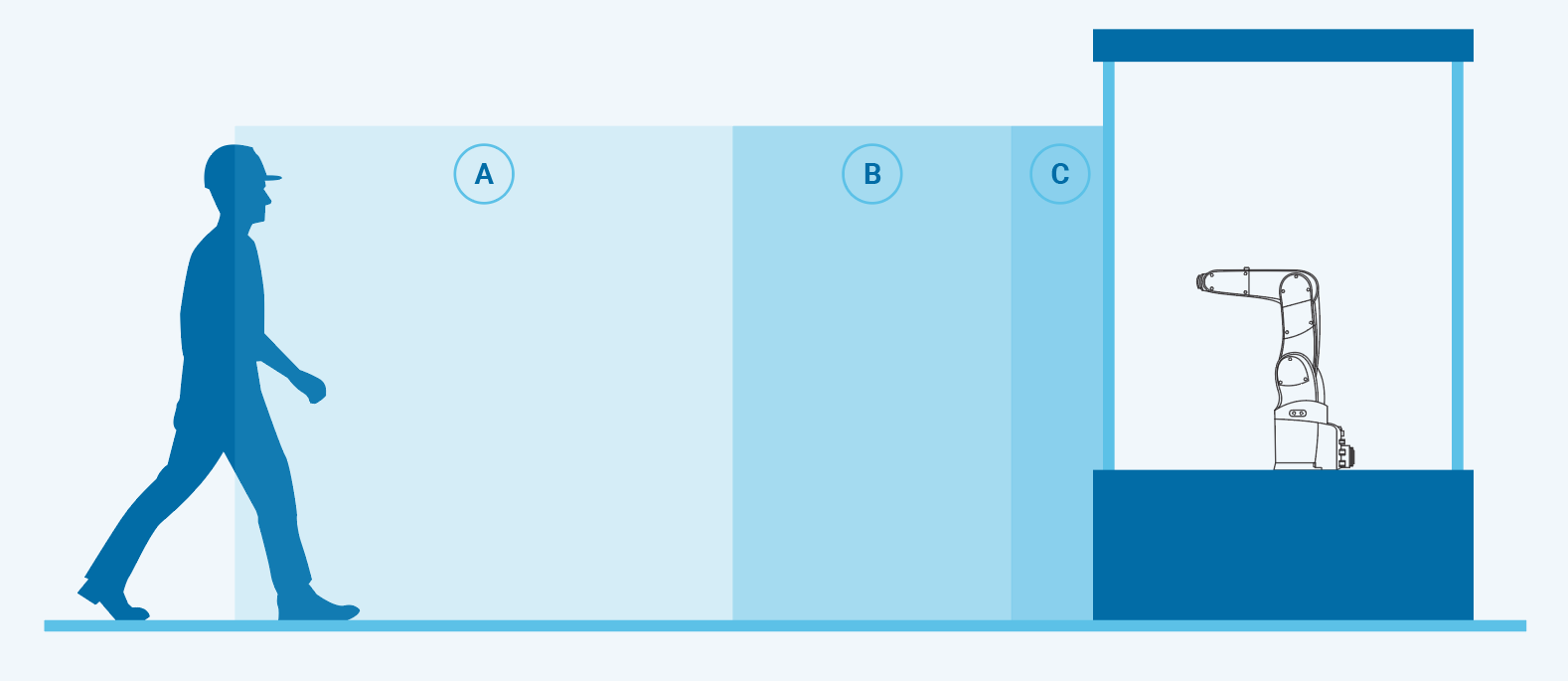
The system uses optical sensors to dynamically control robot speed in relation to the distance of approaching individuals.
Operation-area Monitoring (Zone A)
- Limits robot operation area to personnel working area.
- Personnel and robot can both approach common operation area.
Speed Monitoring (Zone B)
- Limits robot operation speed to safe level when sensor detects personnel entering a specified area.
Stop Monitoring (Zone C)
- Stops robot motion when personnel are detected.
- Returns robot to operation immediate after personnel leave.
Model name | RC8A | |
Power supply | Capacity | 1.8 kVA |
Allowable input voltage range | Three-phase AC200V -15% - AC240V +10% (100 V specification also available for the VP series.) | |
Frequency | Single-phase AC230V -10% - AC240V +10% | |
Power cable length | 5m | |
No. of axes controlled | Robot: 4 to 6 axes Extended-joint: 2 to 4 axes (optional) |
|
Control method | PTP, CP3-dimensional linier, 3-dimensional arc (For SC series and Extended-joints, available PTP control only.) | |
Drive method | All axes all digital AC servo | |
Language in use | DENSO Robotics language (PacScript) | |
Memory capacity | User area Variable area: 1.75MB (32,766 points equivalent) File area: 400MB (5,000 stepsx256 files) |
|
Teaching method | 1) Remote teaching 2) Numerical entry (MDI) 3) Direct teaching (HS series, HM series) |
|
External signal (I/O, etc.) | Universal/dedicated Mini I/O | Input: User open 8 points + System fix 14 points (Safety I/O-less specification: System fix 13 points) 1 Output: User open 8 points + System fix 18 points (Safety I/O-less specification: System fix 12 points) |
Universal/dedicated Hand I/O | Input : User open 8 points Output : User open 8 points |
|
Universal/dedicated Safety Motion | Safety input: 14 points Safety output: 6 points **For Safety Motion specification exclusive use. |
|
DeviceNet slave board (option) | Bus: PCI Express Input : 256 points / Output : 256 points | |
CC-Link remote device board (option) | Bus: PCI Express Input: 128 points / Output: 128 points Remote register Input: 256 points / Output: 256 points |
|
PROFIBUS slave board (option) | Bus: PCI Express Input : 256 points / Output : 256 points | |
EtherNet/IP Adapter board (option) | Bus: PCI Express Input: 4032 points / Output: 4032 points | |
PROFINET IO Device board (option) | Bus: PCI Express Input: 8192 points / Output: 8192 point | |
EtherCAT slave board (option) | Bus: PCI Express Input: 2048 points / Output: 2048 points | |
External communication | RS-232C: 1 line, Ethernet: 1 line (GbE: Gigabit Ethernet), USB: 2 lines, VGA: 1 line (option) | |
Expansion slot | PCI 1 slot PCI Express 1 slot |
|
Self diagnosis function | Overrun, servo error, memory error, input error, short circuit detection (user wiring part) | |
Environmental condition (in motion) | Temperature 0 to 40 degree C, humidity 90% RH or less (dew condensation not allowed) | |
Safety category | Standard type Safety I/O Category4 PL=e Safety Motion Specification Safety I/O Category4 PL=e Safety Motion I/O Category3 PL=d |
|
IP classification | IP20 | |
Approximate weight | Standard: 10kg, Motion: 11kg *2 | |
1 Power for the 100 VAC specification is “Single-phase 100 VAC –5% to 110 VAC +10% 50/60 Hz, 1 kVA. | ||
2 Excludes weight of supplied cables. |
Downloads
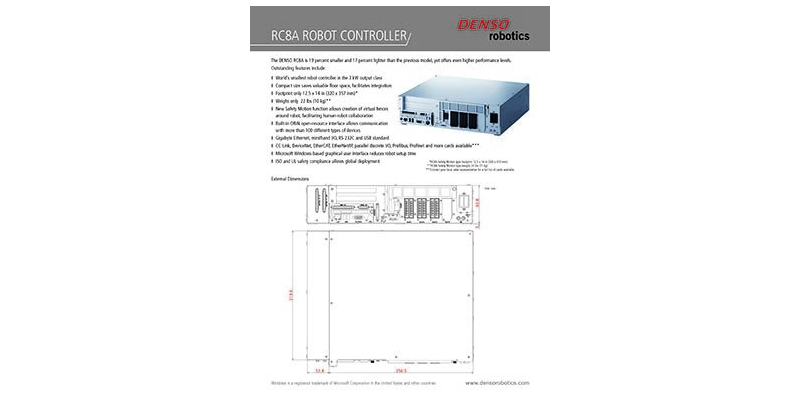
RC8A Controller Product Sheet
Two-page product sheet with features, specifications and dimensions.
- Version
- Download 301
- File Size 0.00 KB
- File Count 1
- Create Date October 15, 2021
- Last Updated October 15, 2021
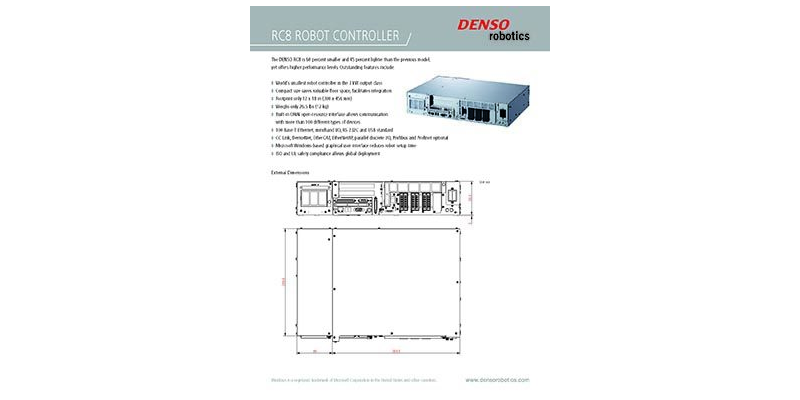
RC8 Controller Product Sheet
Two-page product sheet with features, specifications and dimensions.
- Version
- Download 171
- File Size 0.00 KB
- File Count 1
- Create Date October 15, 2021
- Last Updated October 15, 2021
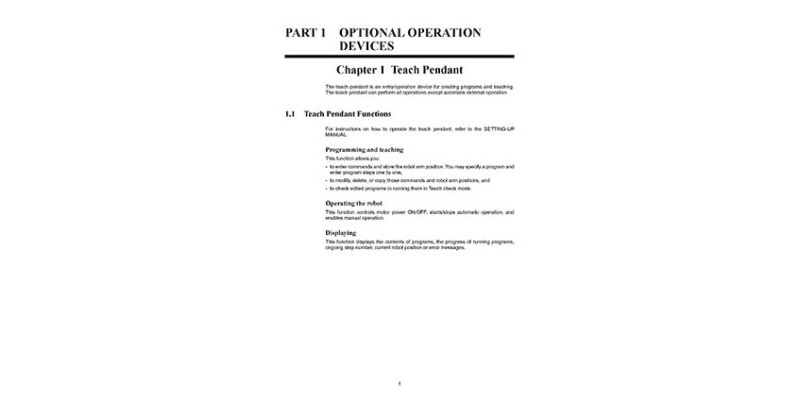
RC7-RC8 Color Pendant Optional Operation Devices
- Version
- Download 129
- File Size 0.00 KB
- File Count 1
- Create Date October 15, 2021
- Last Updated June 9, 2022
CAD Files and Manuals
Find 2D/3D CAD data, application software, PDF manuals, and part lists. (Account registration required)
Online/Interactive Manuals
Account registration required.